Alles für die Qualität.
Produktionsbegleitende Prüfroutinen sowie Funktions- und Leistungstests sichern die Qualität des PANTHER.
Es sind nicht weniger als 50 montagebegleitende Checklisten mit hunderten Prüfpositionen, die im Rahmen der Produktion eines PANTHER abgearbeitet werden müssen. Im Vorfeld bei der Komponenten- und Modulfertigung, beim unmittelbaren Zusammenbau des Fahrzeuges auf der Chassis- und der Aufbaulinie und natürlich am Ende des gesamten Fertigungszyklus, bevor der PANTHER die Freigabe zur Auslieferung an den Kunden erhält. Jede Kontrolle vor, während und nach der Produktion, ob Sichtprüfung, Funktions- oder Leistungstest, wird protokolliert, von einem der ausführenden Monteure oder einem Mitarbeiter aus dem Qualitätsmanagement bestätigt und in einer Datenbank hinterlegt. So wird die Qualität des PANTHER zuverlässig über den gesamten Produktentstehungsprozess von der Bandauflage bis zur Auslieferung gesichert und nachgewiesen.
Am Beispiel Löschtechnik
Das technologische Herz eines PANTHER ist seine Pumpenanlage, bestehend aus Einbaupumpe, Schaumzumischsystem, optionalem Hochdruckaggregat und Druckluftschaumsystem inklusive Verrohrung, Steuerung, Elektrik, Elektronik, Pneumatik ... Schon in der Montagelinie wird die Pumpe als Komponente abgedrückt, um sicherzustellen, dass sie hundertprozentig dicht ist, bevor sie zur Pumpenanlage ausgebaut wird. Das gleiche geschieht dann noch einmal mit der fertig gestellten Pumpenanlage, ehe sie im Prüfzentrum zum ersten Belastungstest antritt. Dort durchläuft sie dann ein festgelegtes Prüfprogramm, bei dem nicht nur eine Reihe von Parametern, allen voran die garantierten Fördermengen, Durchflussraten und Drücke nachgewiesen, sondern auch die Zumischsysteme kundenspezifisch eingestellt und die Ergebnisse protokolliert werden.
Zwei Mal ins Prüfzentrum
Keine Rosenbauer Pumpenanlage verlässt die Fertigung ohne Prüfprotokoll und nur mit diesem Nachweis darf sie in ein Feuerwehrfahrzeug eingebaut werden. Auch die Werfer werden schon im Zuge der Montage elektrisch vorgeprüft und voreingestellt und nur mit Testprotokoll an die PANTHER-Aufbaulinie geliefert. Ist das Fahrzeug dann fertig aufgebaut, kommen Pumpenanlage und Werfer ein weiteres Mal ins Prüfzentrum, diesmal um die Leistungswerte auch im ein- bzw. aufgebauten Zustand zu bestätigen. Auf eigenen Fahrzeugprüfständen werden unter anderem die Ausstoßleistungen und Wurfweiten der Werfer gemessen oder im Schaumbetrieb die Zumischraten, Verschäumungszahlen und Viertelwertszeiten überprüft. Jeder PANTHER ist auf Herz und Nieren funktionsgeprüft, wenn sich die Werkstore hinter ihm schließen.
Qualitätsroutinen im Rahmen der Produktion
Die PANTHER-Montage selbst (der Zusammenbau des Fahrzeuges) erfolgt ausschließlich mit qualitätsgeprüften Komponenten und Modulen. Das gilt für Zukaufteile wie Achsen, Aufhängung und Motor genauso wie für die Aufbaumodule aus der eigenen Fertigung, deren Qualität mittels Checklisten in den einzelnen Produktionsabschnitten bestätigt werden muss. An besonders neuralgischen Stellen im Produktionsdurchlauf sind darüber hinaus Q-Gates mit definierten Testroutinen eingerichtet, um Funktionalität und Qualität von bereits verbauten Teilsystemen überprüfen zu können, bevor am Fahrzeug weitergearbeitet wird.
Eines dieser Q-Gates befindet sich am Ende der Chassislinie, wo das fertige PANTHER-Fahrgestell zum ersten Mal in Betrieb genommen, elektrisch durchgetestet und virtuell Probe gefahren wird. Ein anderes an der Schnittstelle von der Kabinen- zur Aufbaulinie, um die im Cockpit zusammenlaufenden Steuer- und Bediensysteme zu überprüfen, bevor das Modul aufgesetzt wird.
Q-Gates zur Qualitätssicherung
Das wichtigste Q-Gate mit allein rund 140 Prüfpositionen ist am Ende der Aufbaumontage eingerichtet, wo das Gesamtfahrzeug in Betrieb genommen wird. Hier können die Werfer oder ein Löscharm erstmals am Fahrzeug bewegt und die einzelnen Funktionen (Drehbewegung, Schwenkbereich, Umschaltung Werfer/Löscharm ...) geprüft werden. Auch die Steuerungssoftware kann jetzt vollumfänglich durchgecheckt werden, zum Beispiel, ob die Funktionstasten korrekt zugeordnet oder geclusterten Funktionen richtig programmiert sind. Spurbreite, Lenkradeinschlag und die Funktion der Bremsen werden mittels spezieller Diagnosegeräte überprüft, bei Bedarf in eigens dafür ausgestatten Montagegruben nachjustiert und die Werte protokolliert. Darüber hinaus prüft das Qualitätsmanagement an diesem Q-Gate auch, ob die Montagen sauber durchgeführt wurden, alle wasserführenden Leitungen ordentlich isoliert sind, die Elektroanschlüsse konserviert sind, Türen und Rollläden dicht schließen, die Spaltmasse stimmen und insgesamt das Fahrzeug nach den speziellen Kundenwünschen gebaut wurde. Anschließend geht es, wie oben schon erwähnt, ins Prüfzentrum, wo der technische Nachweis der vertraglich zugesicherten Leistung und Qualität erbracht und protokolliert wird.
Am letzten Q-Gate erfolgt die Endkontrolle und dabei wird überprüft, ob sämtliche Checklisten korrekt abgearbeitet und allfällige Finisharbeiten erledigt worden sind. Außerdem wird das Fahrzeug nochmals einer finalen Sichtprüfung unterzogen, bevor es gereinigt und auf Hochglanz poliert dem Kunden übergeben werden kann.
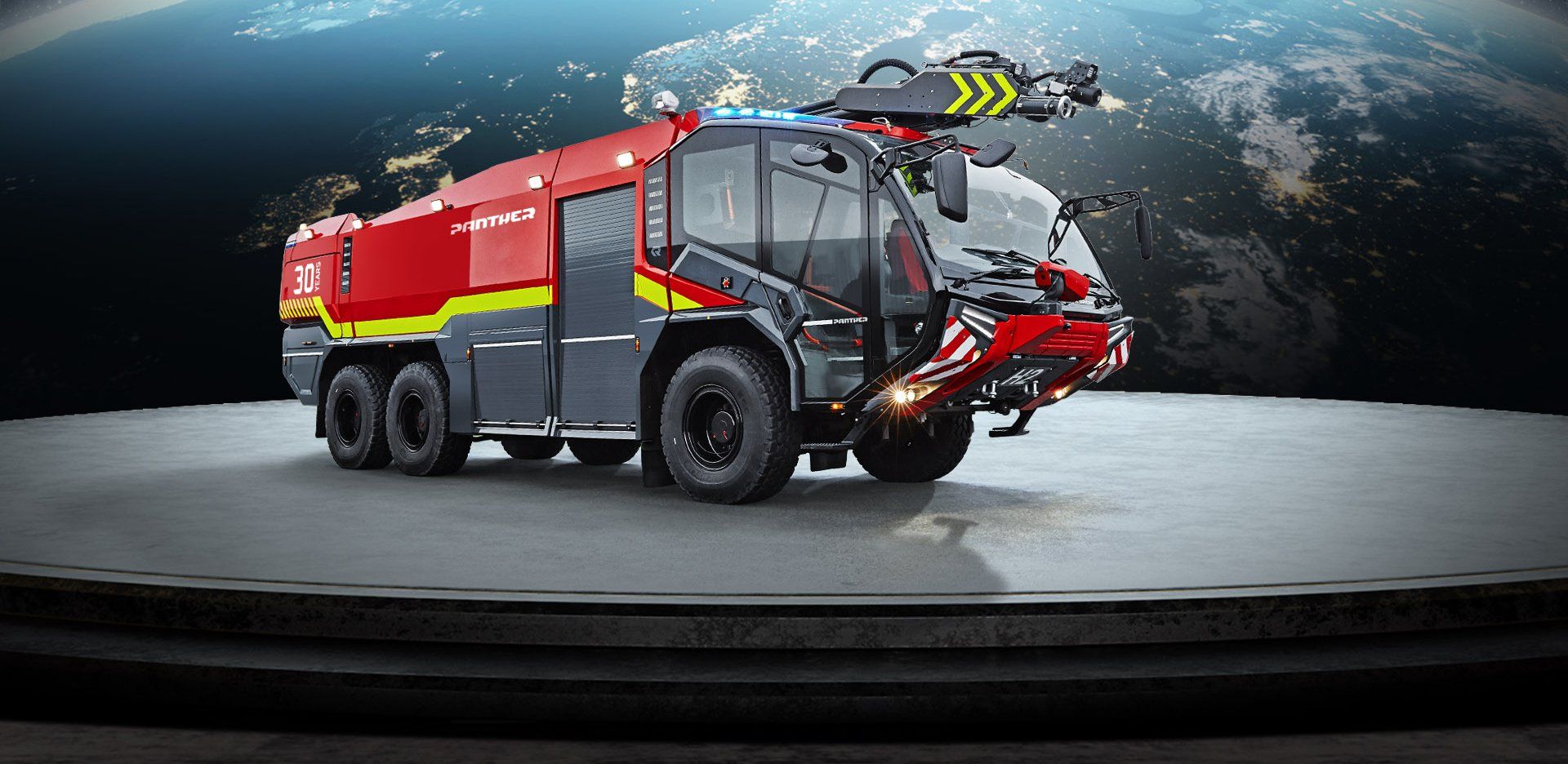
Jetzt zum Rosenbauer Newsletter anmelden & immer bestens informiert sein!
Kontakt
Rosenbauer International AG
Paschinger Str. 90
4060 Leonding, Österreich
office@rosenbauer.com