Alles auf Linie.
Der Blick hinter die Kulissen der Produktion zeigt, wie ein PANTHER entsteht.
Die Werkstore öffnen sich, ein soeben fertig gestellter PANTHER 6x6 verlässt blitzblank poliert und mit eingeschaltetem Blaulicht die Produktion. Die Montageteams haben ganze Arbeit geleistet und auf zwei getakteten und synchronisierten Linien (Chassis und Aufbau) mit sequentieller Materialversorgung innerhalb von 67 Tagen ein Feuerwehrfahrzeug der Superlative geschaffen. Aber alles der Reihe nach ....
Vom Grundrahmen zum „Running Chassis“
Die Arbeiten an einem PANTHER beginnen beim Grundrahmen, einer verwindungssteifen Tragekonstruktion aus hochfesten Stahlprofilen, aufgebockt auf Station 1 der Chassislinie. An diesen Rahmen wird in einem ersten Schritt alles angebaut, was zum Fahrwerk gehört: Allrad-Achssystem, Schraubenfedern, Stoßdämpfer, Längs- und Querlenker, Gelenkwellen, Stabilisatoren usw. Auch Teile der Lenkung und der Bremsanlage werden hier schon montiert, bevor das Rohchassis seine feuerfeste Lackierung erhält.
In weiteren Arbeitsschritten werden auf den Grundrahmen Motor, Auspuffanlage, Kraftstofftank und Kühlerpaket aufgesetzt sowie die zugehörigen Kabelbäume und Medienleitungen verlegt und verbunden. Am Ende der Chassislinie erfolgt die Montage der Reifen, die Motorsoftware wird eingespielt, das Antriebsaggregat kalibiriert und die Betriebsflüssigkeiten werden eingefüllt. Damit ist das „Running Chassis“, quasi die untere Hälfte des PANTHER, fertig und es kann in Betrieb genommen und durchgecheckt werden (STALL-Test). Es folgt eine erste, kurze Test- und Funktionsfahrt, anschließend wird das Fahrgestell in die Aufbaulinie eingeschleust, wo die obere Hälfte des PANTHER entsteht.
Aufbau mit anschlussfertigen Modulen
Vier Module bilden den Aufbau eines PANTHER: Fahrerhaus und Mannschaftskabine, Pumpenraum-, Tank- und Heckmodul. Sie sind bei ihrer Anlieferung an die Linie so weit ausgebaut und vorgefertigt, wie es angesichts der kundenspezifischen Komplexität der Fahrzeuge möglich und der Effizienz und Ergonomie der Montage förderlich ist. In Fahrerhaus und Mannschaftsraum sind beispielsweise schon alle Bildschirme und Bedienelemente verbaut und verkabelt und müssen nur mehr mit der Chassiselektronik verbunden werden. Klimaanlage, Heizung, PA-Halter sowie die Konsolen für Ablagen und Sitze sind ebenfalls bereits montiert, gleiches gilt für die Rundumkennleuchten und die Dachbeleuchtung. Das Pumpenraummodul wiederum ist mit der kompletten Pumpenanlage samt Grundverrohrung ausgestattet, die Rollladenverschlüsse sind eingebaut, genauso wie der Lichtmast, sofern spezifiziert. Am Tankmodul sind Fludometer (Füllstandsanzeige außen) und Umfeldbeleuchtung angebracht und verkabelt, das Heckmodul kommt mit montierter Heckleiter und Dachbeleuchtung an die Linie, um nur einige Beispiele zu nennen.
„Hochzeit“ und weiterer Ausbau
Der erste Arbeitsschritt an der PANTHER Aufbaulinie ist die Vorbereitung des Chassis auf das Aufsetzen der Module. Dazu gehört zum Beispiel der Einbau der Gelenkwelle für den Pumpenantrieb oder die Verlegung der Leitungen für den Frontwerfer und die Bodensprühdüsen der Deluge-Anlage. Im zweiten Arbeitsschritt werden die vier Module der Reihe nach mit dem Chassis „verheiratet“, sprich auf den Grundrahmen aufgesetzt, ausgerichtet, elektrisch angeschlossen und verbunden. Aufgrund ihres hohen Vorfertigungsgrades lässt sich diese Arbeit an einer Station (innerhalb eines Taktes) erledigen.
Mit aufgesetzten Modulen kann nun weiter an- und ausgebaut werden: Front- und Dachwerfer werden am Kabinenmodul montiert und alle wasserführenden Leitungen zwischen Tank und Pumpenraum sowie zu den Haspeln, Druck- und Werferabgängen komplettiert und abgedichtet. Auch der Anbau bestimmter Karosserieteile und der gesamte Innenausbau sind jetzt möglich, zum Beispiel die Montage der Stoßstangen und des Unterfahrschutzes an das Kabinen- und das Heckmodul, der Anbau der Gerätetiefräume unter dem Sichttank, das Anbringen der Absturzsicherungen am Dach sowie der Einbau von Steckdosen, Ladehalterungen, Schlauchfächer und aller benötigten Halterungen für Strahlrohre, Druckluftflaschen, Feuerlöscher, Werkzeuge etc. im Fahrzeug.
IBN und Übergabe ans Qualitätsmanagement
Sobald die Module mit den An- und Ausbauten versehen und alle elektrischen, elektronischen (CAN) und wasserführenden Leitungen verbunden sind, wird die Steuerungssoftware eingespielt und werden bestimmte Funktionen (z.B. Gaspedal, Werferbedienung) geteacht, sprich eingelernt. Danach geht der fertig aufgebaute PANTHER an die letzte Station zur Inbetriebnahme. Der Motor wird (ein zweites Mal) gestartet und nun das Gesamtfahrzeug durchgecheckt, zum Beispiel, ob sich Werfer und Löscharm in vollem Umfang bewegen lassen, ob Scheinwerfer und Umfeldbeleuchtung richtig eingestellt sind oder die Tastenbelegung am Steuerungsdisplay stimmt. Anschließend wird die zu halternde Ausrüstung vervollständig, das Fahrzeug innen und außen gereinigt und der PANTHER an das Qualitätsmanagement übergeben, wo er auf Herz und Nieren geprüft wird und seine löschtechnische Leistung auf Prüfständen unter Beweis stellen muss, bevor er die Freigabe zur Auslieferung erhält.
Rosenbauer produziert das Flaggschiff seiner Flughafenlöschfahrzeugflotte an zwei Fertigungsstandorten, in der österreichischen Konzernzentrale (Werk Leonding II) und im amerikanischen Wyoming (Werk Minnesota). Hier wie dort sichern industrielle Produktionsstandards der Automobilbranche nicht nur eine möglichst effiziente Montage mit kurzen Durchlaufzeiten sondern vor allem die an ein derartiges Highend-Produkt gestellten Anforderungen nach größtmöglicher Zuverlässigkeit und Sicherheit.
Ein Einblick in die PANTHER Produktion am Standort Leonding.
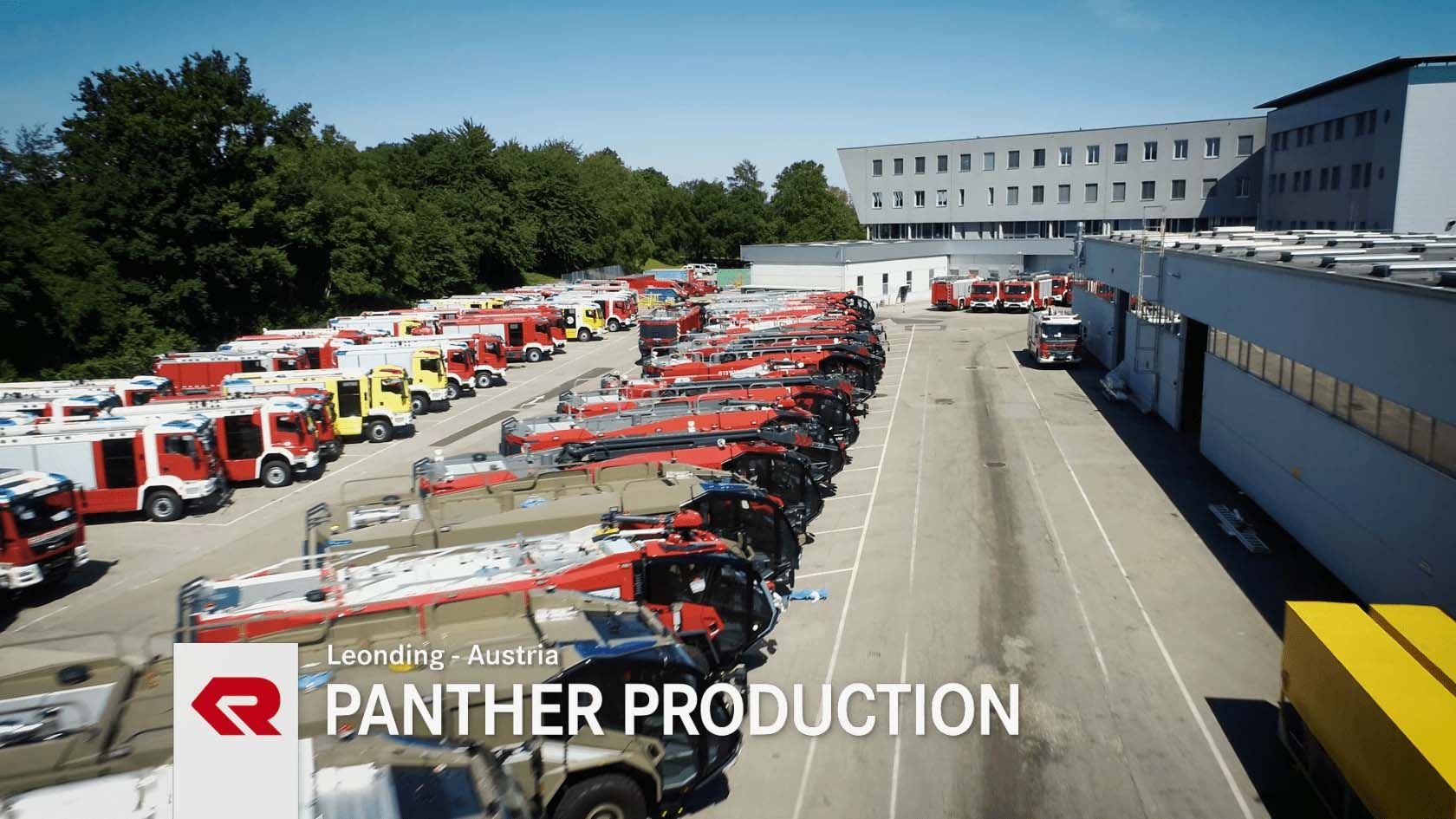
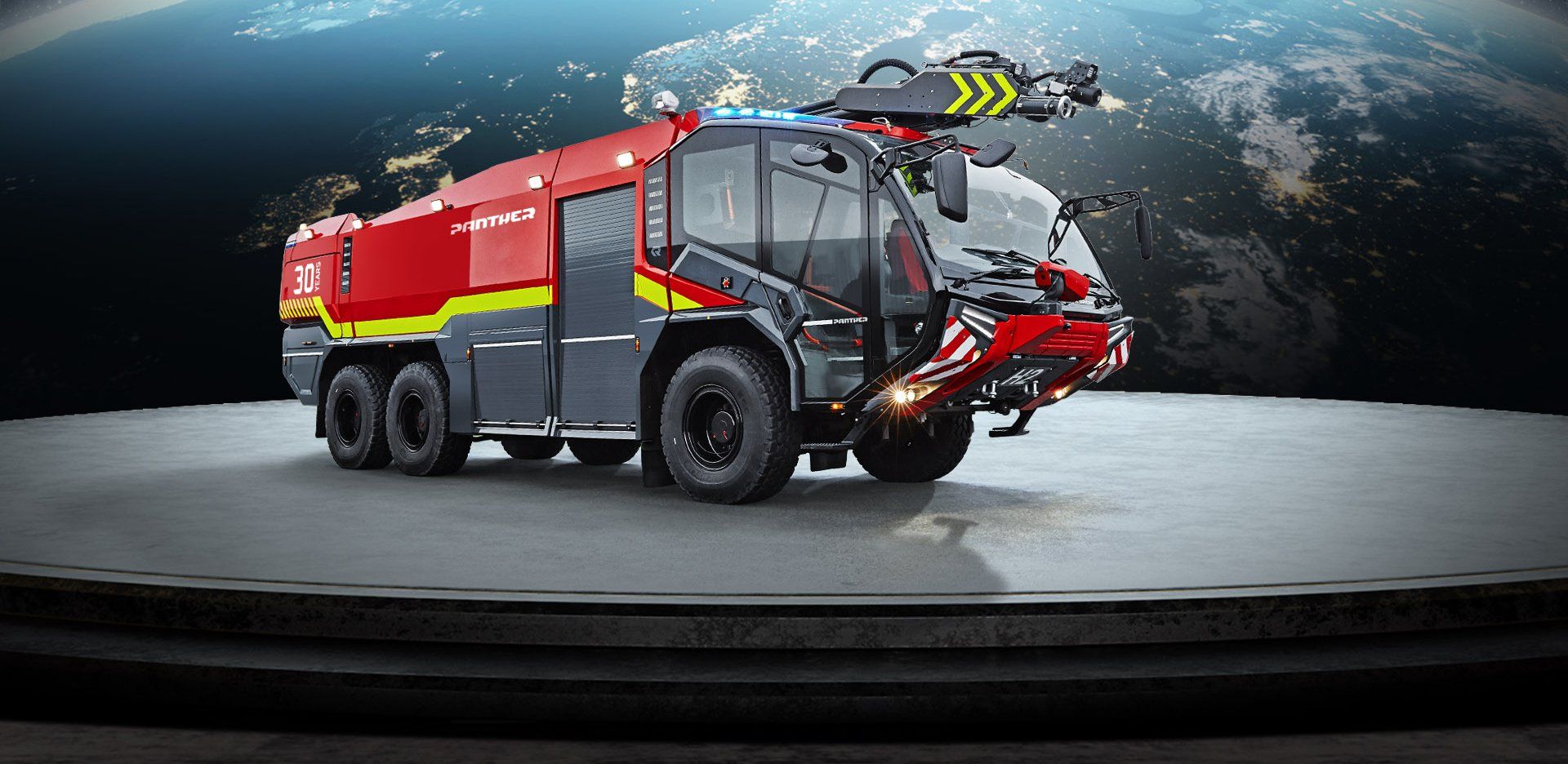
Jetzt zum Rosenbauer Newsletter anmelden & immer bestens informiert sein!
Kontakt
Rosenbauer International AG
Paschinger Str. 90
4060 Leonding, Österreich
office@rosenbauer.com