Everything on line.
A look behind the scenes of production shows how a PANTHER is made.
The factory gates open and a PANTHER 6x6 that has just been completed leaves the production line brightly polished and with its blue lights switched on. The assembly teams have done a great job and created a superlative fire fighting vehicle on two synchronized lines (chassis and body) with sequential material supply within 67 days. But everything in sequence ....
From the base frame to the "running chassis"
Work on a PANTHER starts with the base frame, a torsionally rigid supporting structure made of high-strength steel sections, jacked up at station 1 of the chassis line. In a first step, everything that belongs to the chassis is attached to this frame: all-wheel axle system, coil springs, shock absorbers, longitudinal and transverse control arms, propeller shafts, stabilizers, etc. Parts of the steering and braking systems are also assembled here before the unfinished chassis receives its fireproof paint finish.
In further work steps, the engine, exhaust system, fuel tank and radiator package are mounted on the base frame and the associated wiring harnesses and media lines are laid and connected. At the end of the chassis line, the tires are fitted, the engine software is installed, the drive unit is calibrated and the operating fluids are filled. This completes the running chassis, the lower half of the PANTHER, so to speak, and it can be put into operation and checked through (STALL test). This is followed by an initial, short test and functional run, after which the chassis is fed into the build-up line, where the upper half of the PANTHER is created.
Assembly with ready-to-connect modules
Four modules make up the body of a PANTHER: driver's cab and crew cabin, pump room module, tank module and rear module. When they are delivered to the line, they are expanded and prefabricated to the extent possible in view of the customer-specific complexity of the vehicles and conducive to assembly efficiency and ergonomics. In the driver's cab and crew compartment, for example, all screens and controls are already installed and wired and only need to be connected to the chassis electronics. Air conditioning, heating, PA holders and the consoles for storage compartments and seats are also already fitted, as are the rotating beacons and roof lighting. The pump room module, in turn, is equipped with the complete pump system including basic piping, the shutter closures are installed, as is the light pole, if specified. On the tank module, the fludometer (external level indicator) and ambient lighting are fitted and wired, and the rear module comes to the line with the rear ladder and roof lighting fitted, to name just a few examples.
"Wedding" and further expansion
The first work step on the PANTHER body line is to prepare the chassis for mounting the modules. This includes, for example, the installation of the PTO shaft for the pump drive or the routing of the lines for the front launcher and the ground spray nozzles of the Deluge system. In the second work step, the four modules are "married" to the chassis one after the other, i.e. placed on the base frame, aligned, electrically connected and connected. Due to their high degree of prefabrication, this work can be completed at one station (within one cycle).
With the modules in place, further additions and extensions can now be made: Front and roof-mounted launchers are fitted to the cab module, and all water-carrying lines between the tank and pump room and to the reels, pressure and launcher outlets are completed and sealed. It is also now possible to attach certain body parts and complete the interior work, for example, mounting the bumpers and underride guard to the cab and rear modules, attaching the equipment compartments under the sight tank, attaching the fall protection devices to the roof, and installing sockets, load holders, hose compartments, and all the necessary holders for jet pipes, compressed air bottles, fire extinguishers, tools, etc. in the vehicle.
IBN and handover to quality management
As soon as the modules are equipped with the attachments and extensions and all electrical, electronic (CAN) and water lines are connected, the control software is installed and certain functions (e.g. accelerator pedal, launcher operation) are taught. After that, the completely assembled PANTHER goes to the last station for commissioning. The engine is started (a second time) and the entire vehicle is checked, for example, whether the launcher and extinguishing arm can be moved to their full extent, whether the headlights and ambient lighting are set correctly or whether the key assignment on the control display is correct. The equipment to be stored is then completed, the vehicle is cleaned inside and out, and the PANTHER is handed over to quality management, where it is put through its paces and has to prove its extinguishing performance on test rigs before it is approved for delivery.
Rosenbauer produces the flagship of its airport fire fighting vehicle fleet at two manufacturing sites, at the Austrian Group headquarters (Leonding II plant) and in Wyoming, USA (Minnesota plant). Here, as there, industrial production standards of the automotive industry ensure not only the most efficient assembly possible with short throughput times, but above all the requirements placed on such a high-end product for the greatest possible reliability and safety.
An insight into PANTHER production at plant Leonding.
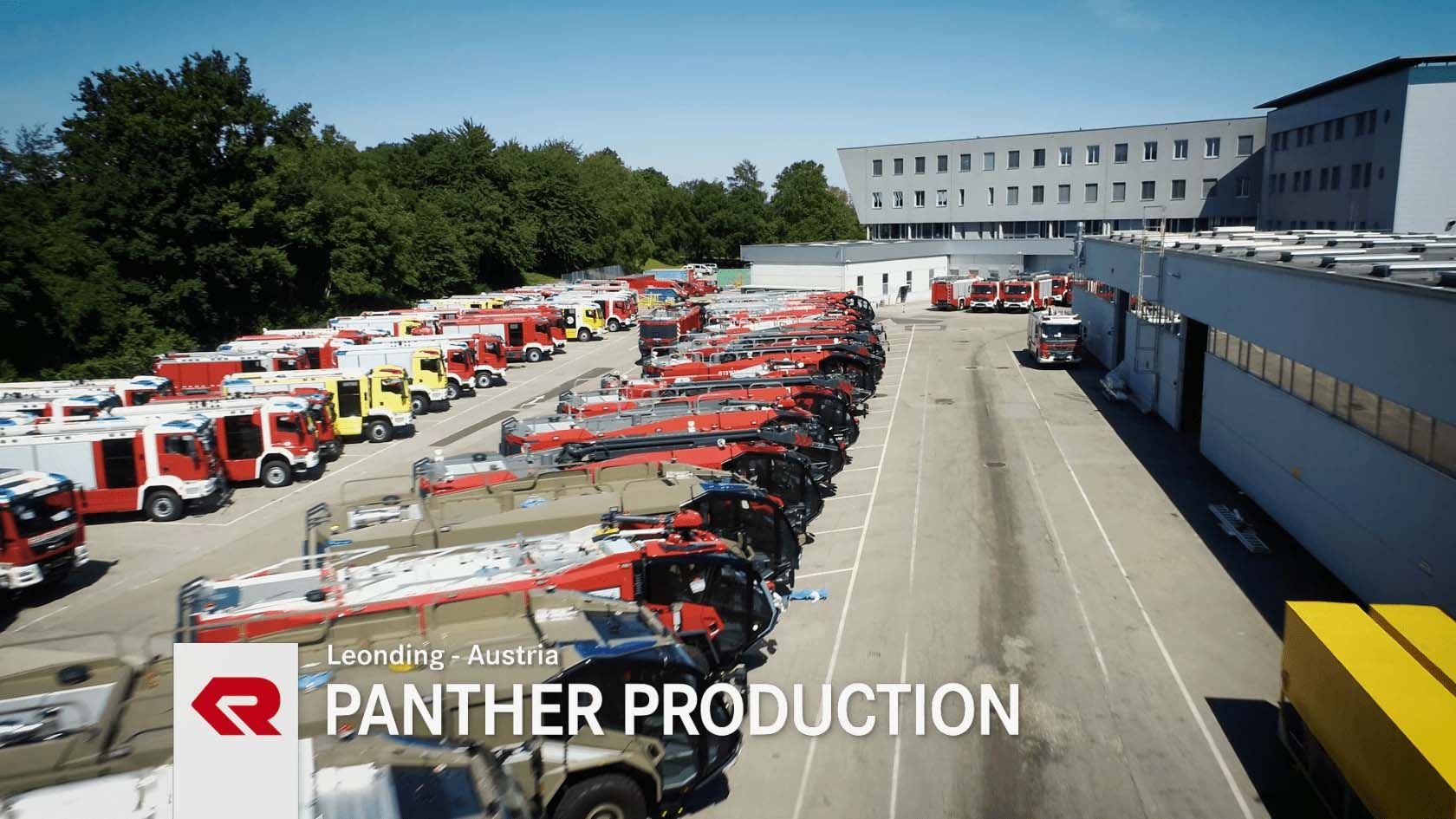
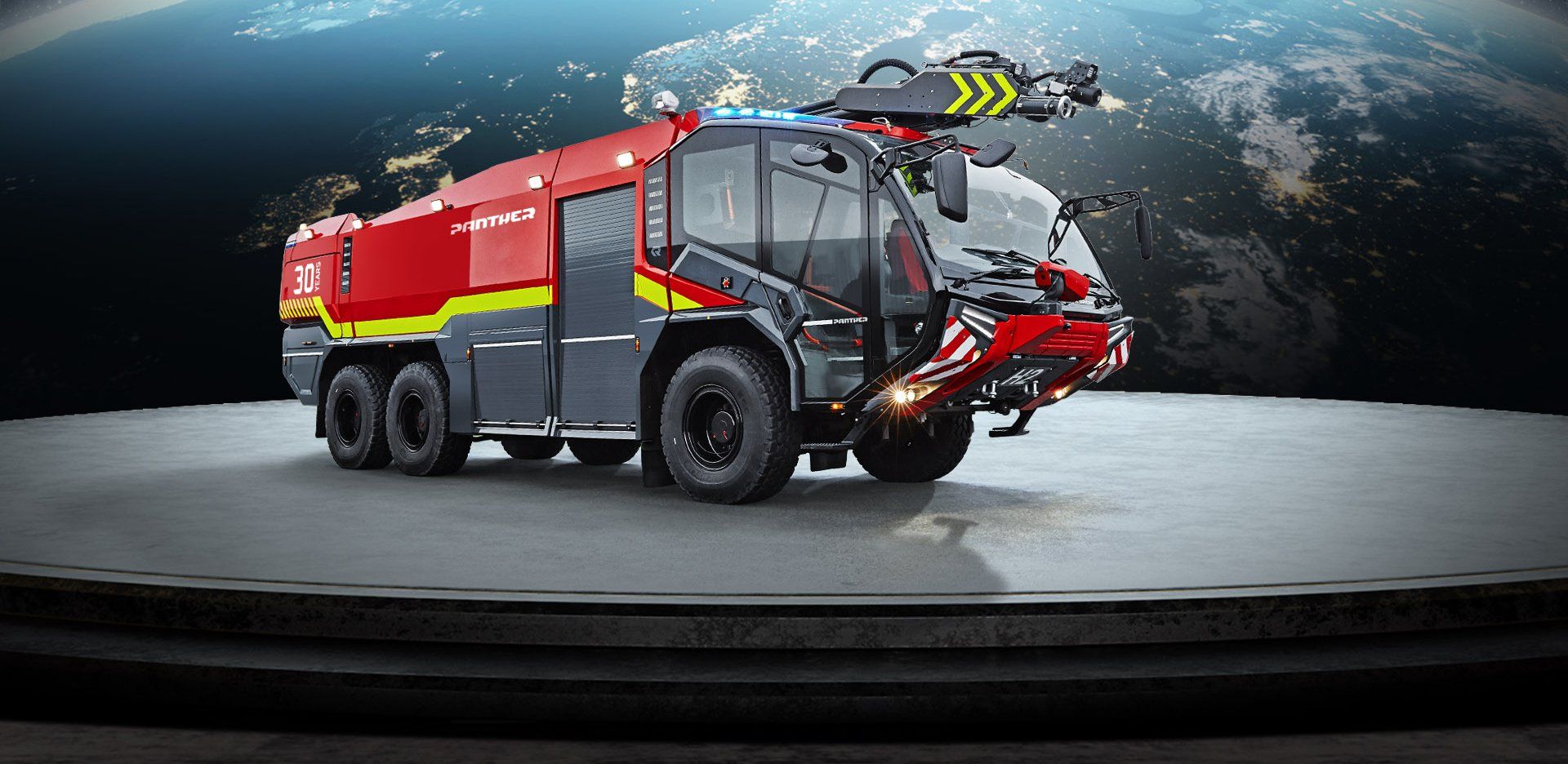
Register now for the Rosenbauer Newsletter & always be well informed!
Contact
Rosenbauer International AG
Paschinger Str. 90
4060 Leonding, Austria
office@rosenbauer.com