Everything for quality.
In-process testing routines as well as functional and performance tests ensure the quality of the PANTHER.
No fewer than 50 assembly-related checklists with hundreds of test items have to be processed during the production of a PANTHER. In the run-up to component and module production, during the immediate assembly of the vehicle on the chassis and body lines, and of course at the end of the entire production cycle before the PANTHER is released for delivery to the customer. Every check before, during and after production, whether visual inspection, functional or performance test, is logged, confirmed by one of the assemblers carrying out the work or by a member of the quality management team, and stored in a database. In this way, the quality of the PANTHER is reliably ensured and verified throughout the entire product development process, from the belt support to the delivery.
The example of extinguishing technology
The technological heart of a PANTHER is its pump system, consisting of a built-in pump, foam proportioning system, optional high-pressure unit and compressed-air foam system, including piping, control system, electrics, electronics, pneumatics ... Already in the assembly line, the pump is pressure tested as a component to ensure that it is one hundred percent leak-proof before it is removed to form the pump system. The same procedure is then repeated with the completed pump system before it is subjected to its first load test in the test center. There, it is subjected to a defined test program that not only verifies a number of parameters, first and foremost the guaranteed flow rates, flow rates, and pressures, but also adjusts the proportioning systems to customer specifications and records the results.
Twice to the test center
No Rosenbauer pump system leaves production without a test report, and only with this proof may it be installed in a firefighting vehicle. Even the launchers are electrically pretested and preset during assembly and are only delivered to the PANTHER assembly line with a test protocol. Once the vehicle is fully assembled, the pump system and the launcher are sent to the test center once again, this time to confirm the performance values in the installed or assembled state. On the company's own vehicle test rigs, the output rates and throw distances of the throwers are measured, for example, or the proportioning rates, foaming rates and quarter times in foam operation are checked. Every PANTHER is put through its paces when the factory gates close behind it.
Quality routines during production
PANTHER assembly itself (the assembly of the vehicle) is carried out exclusively with quality-tested components and modules. This applies to bought-in parts such as axles, suspension and engine as well as to the body modules from our own production, the quality of which must be confirmed by means of checklists in the individual production stages. Q-gates with defined test routines have also been set up at particularly critical points in the production process to check the functionality and quality of subsystems that have already been installed before work continues on the vehicle.
One of these Q gates is located at the end of the chassis line, where the finished PANTHER chassis is put into operation for the first time, electrically tested and virtually test-driven. Another is at the interface from the cab to the body line to check the control and operating systems converging in the cockpit before the module is mounted.
Q-gates for quality assurance
DThe most important Q-gate, with around 140 test positions alone, is set up at the end of body assembly, where the complete vehicle is put into operation. Here, the launcher or an extinguishing arm can be moved on the vehicle for the first time and the individual functions (rotary movement, swivel range, switching between launcher and extinguishing arm ...) can be tested. The control software can now also be fully checked, for example, whether the function keys are correctly assigned or clustered functions are correctly programmed. The track width, steering wheel angle and brake function are checked using special diagnostic equipment, readjusted if necessary in specially equipped assembly pits and the values are logged. In addition, quality management also checks at this Q-gate whether the assembly work has been carried out cleanly, all water-carrying lines are properly insulated, the electrical connections are preserved, doors and shutters close tightly, the gap dimensions are correct, and overall the vehicle has been built according to the customer's special requirements. As mentioned above, the vehicle then goes to the test center, where technical proof of the contractually guaranteed performance and quality is provided and recorded.
The final inspection takes place at the last Q-gate, where it is checked whether all checklists have been correctly processed and any finishing work has been completed. The vehicle is also subjected to a final visual inspection before it is cleaned and polished to a high gloss before being handed over to the customer.
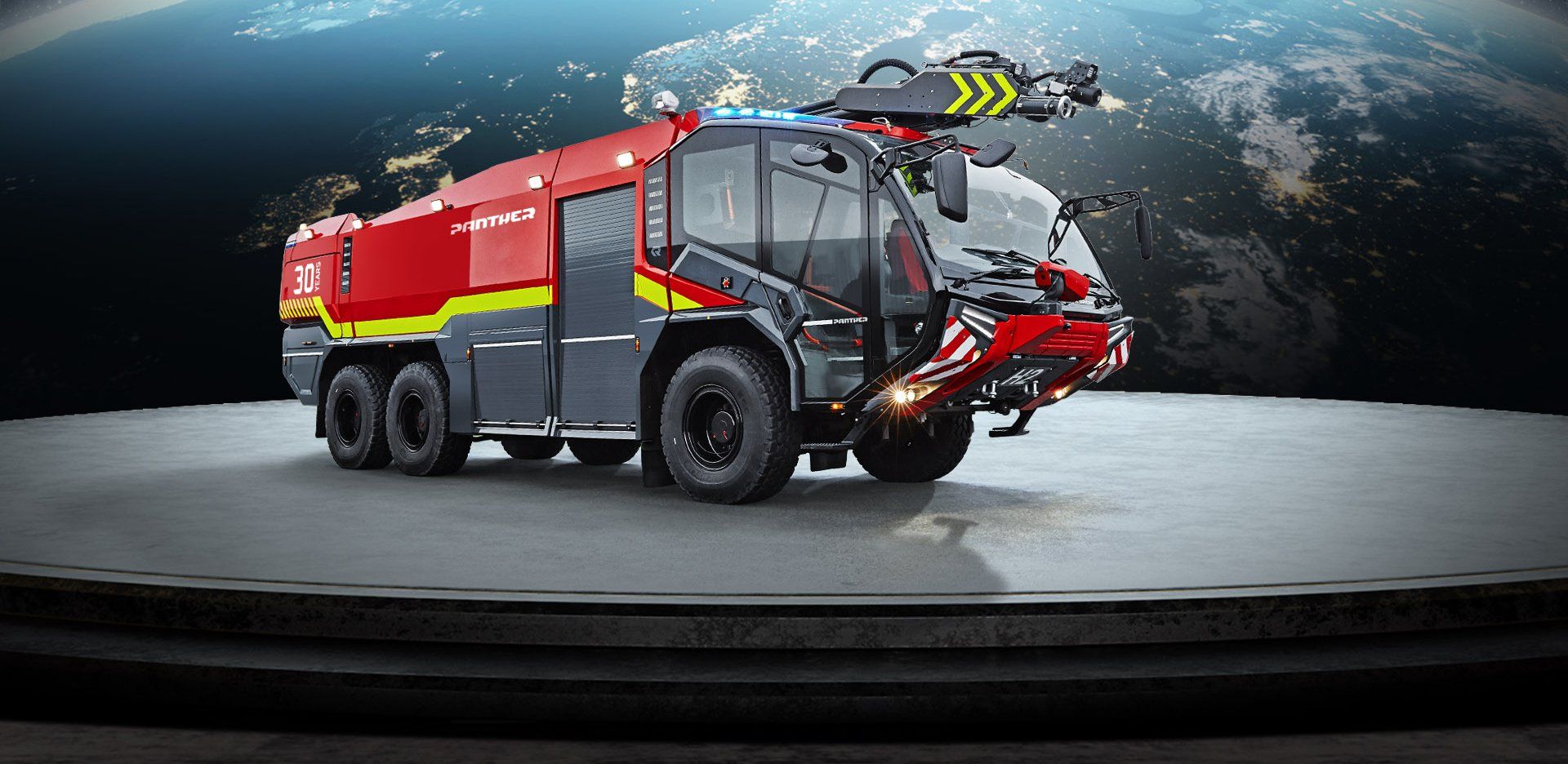
Register now for the Rosenbauer Newsletter & always be well informed!
Contact
Rosenbauer International AG
Paschinger Str. 90
4060 Leonding, Austria
office@rosenbauer.com