From wooden model to multi-body simulation
Time lapse of PANTHER development with computer-aided design.
When Helmut Peherstorfer, a designer from the early days, reflects on the PANTHER's development 30 years ago, he smiles: "We had already swapped the drawing board for the computer, at least in part, but we were still designing in 2D and had endless paper blueprints. That still had very little to do with what we understand today as 3D CAD engineering. Especially when it came to representing the third dimension, there was no getting around analogue technology. Helmut Peherstorfer: "Model and prototype construction played a central role. We approached the final design of the original PANTHER via a wide variety of physical models in scales up to 1:10, and even built the crew cabin in its original size as a wooden model, so that we could accurately assess and adjust the intersections of the various surfaces and radii." The resulting sample models ultimately formed the basis for the construction and quotation drawings.
Initial strength calculations
The second PANTHER generation released at the end of the 1990s was already created entirely on the PC - and in 3D. "The software got better, and so did we as users," says Erwin Affenzeller, who, like Helmut Peherstorfer, is one of the principals in the PANTHER construction. Models were and are still being built today, but the benefits of the virtual representation were convincing: the three-dimensional view of a component could now be generated via software and changes could be visualized immediately. At the same time, the CAD models were used to create the data basis for numerous subsequent processes, for example to control the CNC machine tools in production. In addition, material properties were introduced into the models, which meant that, starting from the digital design, calculations and analyses could now also be carried out using the finite element method (FEM). Erwin Affenzeller: "This made it possible to check whether designed components and structures had the required strength and stiffness, and these could be quickly optimized digitally if necessary. The first virtual crash calculations with the crew cabin were also possible, as well as ergonomic considerations already implemented in digital mockup processes."
Dynamic component simulations
The age of dynamic component testing began with the third PANTHER generation. Wolfgang Luftensteiner, Head of Chassis Development, recalls: "In 2008, it was a matter of increasing the permissible axle weights of the PANTHER 6x6 in order to be able to equip it with the previously newly developed extinguishing arm. The entire chassis was revised and, for the first time, multi-body simulations were used to test how the individual components and subsystems behave under dynamic loads, what interactions occur between the components, and how the overall system interacts.
This was the decisive breakthrough in 3D CAD engineering and is still used today. Wolfgang Luftensteiner: "The challenge with the PANTHER was and is to design this highly dynamic system of large masses and high speeds in such a way that it can be safely and reliably controlled by the emergency crews in extreme situations. Through multi-body simulations, we know how the individual subsystems and the entire vehicle behave under a wide range of loads and can optimize each component from the point of view of increasing performance."
The path to the finished PANTHER.
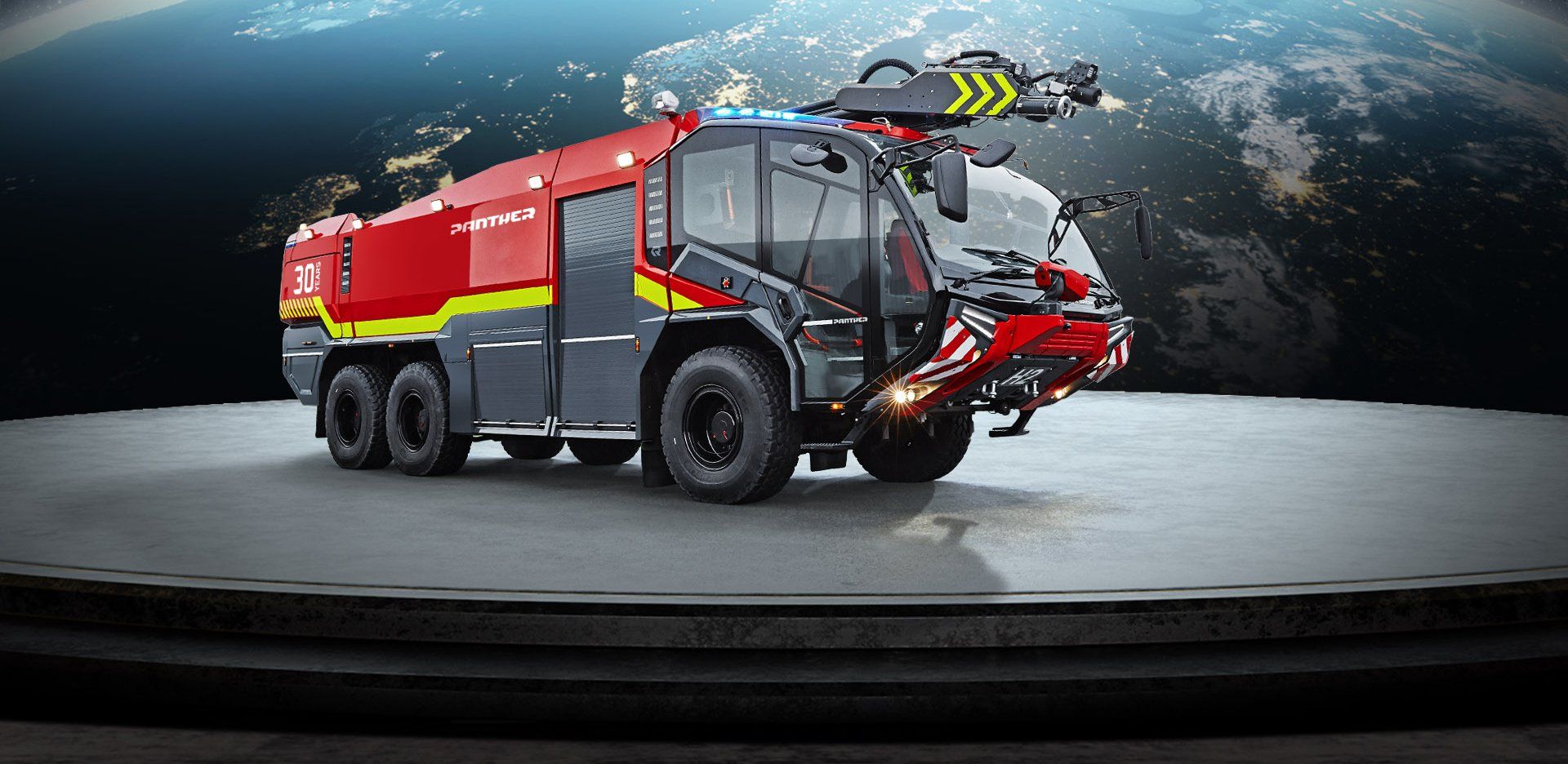
Register now for the Rosenbauer Newsletter & always be well informed!
Contact
Rosenbauer International AG
Paschinger Str. 90
4060 Leonding, Austria
office@rosenbauer.com