Safely around the turn.
Before a new PANTHER receives production approval, the prototype has to prove itself on the test track.
Anyone driving a PANTHER 8x8 at full operational speed into a curve feels the load change in the pit of their stomach. A normal truck would be knocked flat by this weight (up to 52 t) and speed (approx. 90 km/h), but the PANTHER must not be "thrown off track" by such loads. According to the specifications of the International Civil Aviation Organization (ICAO), its lateral stability must also be proven accordingly. For this purpose, the vehicle is placed on a tipping platform and the wheels must bring a defined residual contact weight to the ground, depending on the tipping angle. Rosenbauer does not rely solely on this static rollover test, however. Cornering stability and driving safety are additionally checked and proven in dynamic tests as part of vehicle development. Not only on the road, but also on test tracks with all the "chicanes".
50 hours of continuous testing
Every prototype of a new PANTHER completes an extreme rally before it receives series production approval. For this purpose, Rosenbauer uses a closed-off test track around nine kilometers long not far from the Group headquarters. The first kilometers are asphalted and perfectly suited to acceleration, emergency braking and other defined maneuvers such as circling or fast lane changes. Then it's off to a circuit with bad roads and potholes, uphill hills and wading pools, as well as over a natural twisting track and jogging track. This is ideal for testing the PANTHER's all-wheel-drive capabilities, its approach on steep terrain, its directional stability on boggy ground, and also the rigidity of the body and its tightness.
A lap lasts around 20 minutes, two at a time, after which the prototype is subjected to a visual inspection and the measurement data such as acceleration, steering wheel angle, brake pressures, wheel speeds, etc. recorded by the driving test laboratory during the extreme rally are read out and logged via the CAN bus. The subjective impressions of the test drivers, keyword: popometer, are also included in the assessment of the driving behavior and, together with the sensor data, contribute to the tuning of the vehicle. At least a hundred such test cycles are completed, by which time around 50 hours of continuous use have been reached, thus simulating practically a complete product life cycle.
Assistant intervenes
Extensive testing was also part of the development of the electronic driving stability system for the PANTHER. This system detects movements around the vehicle's vertical (skidding) and longitudinal axes (rolling, tipping) and automatically intervenes if dynamic driving limits are exceeded. Depending on the steering angle and the vehicle speed, the engine torque is first reduced and, if that is not enough, active braking intervention is carried out wheel by wheel. The strength and sensitivity with which the system should intervene to provide sensible support for inexperienced drivers and not patronize experienced drivers was determined on special test routes: The high-speed and high-friction tests were run in Jeversen, Germany, while the tests on snow and ice (low friction coefficient) took place in Rovaniemi, Finland.
Tests in accredited laboratories
A number of functional and safety checks are carried out in external, accredited testing laboratories. This applies, for example, to the structural rigidity of the cabin, which is verified in crash tests in accordance with ECE (UN) R29, electromagnetic compatibility and interference immunity, the strength of the vehicle lighting, and noise emissions.
The extinguishing technology installed in the PANTHER is also fully tested and equipped with test protocols. Their performance is verified on the pump and vehicle test rigs in the company's own test centers and during test drives on closed routes with verifiable documentation. At the customer's request, the performance data are additionally confirmed during acceptance tests and so-called factory acceptance tests.
The PANTHER is a fully integrated system of precisely matched chassis, body and firefighting technology components that are subjected individually and as a complete vehicle to the highest stresses and defined test scenarios before a prototype is launched on the market.
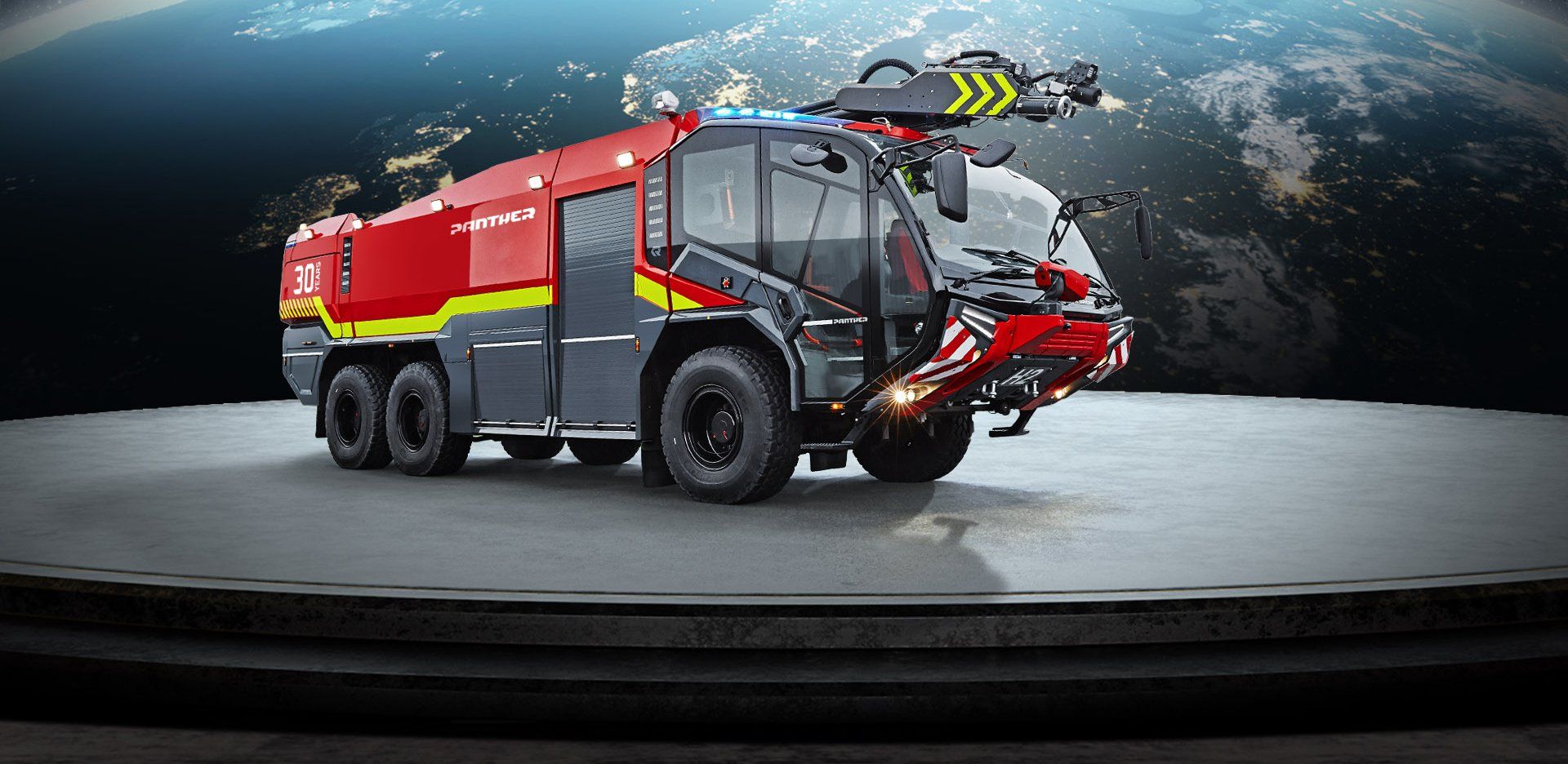
Register now for the Rosenbauer Newsletter & always be well informed!
Contact
Rosenbauer International AG
Paschinger Str. 90
4060 Leonding, Austria
office@rosenbauer.com