Technology teaches humility.
Wolfgang Luftensteiner, Head of PANTHER chassis development, on the engineering of aircraft rescue and fire fighting (ARFF) vehicles.
Mr Luftensteiner, do you remember your first major engineering assignment with the PANTHER?
Wolfgang Luftensteiner:Yes, of course, that was the further development of the 6x6 chassis from 36 to 39 tonnes total weight eleven years ago, after I had already been involved in the redesign of the boom. In order to achieve the higher axle loads we were aiming for, we had to rework the entire chassis, from the frame to the axles, springs, shock absorbers, brakes right down to the steering system.
How did you go about it, what is the basic engineering process for the PANTHER?
Wolfgang Luftensteiner:Basically, not very different from any other technical development. We create a setup in which we define the theoretical requirements that a newly designed component or a newly developed subsystem must fulfill. Then we clarify, develop, and construct. We use finite element calculations to check whether the components and systems have the required strength and stiffness. Through multi-body simulation, we evaluate the driving dynamics on a virtual vehicle model. After an extensive test phase, the parts and systems are subsequently optimized and transferred to series production. Incidentally, multi-body simulation was used for the very first time during the aforementioned chassis conversion; today it is standard at Rosenbauer and an integral part of the engineering process.
What are the special challenges for the engineering of ARFF vehicles?
We are responsible for providing the airport fire departments with a tool that they must be able to operate safely and reliably under extreme operating conditions, high stress levels, and tight timescales. This tool is a very dynamic and complex system that can only be mastered by understanding it in its entirety and getting to the bottom of every technical design question. This means that our thoroughness correlates directly with the safety of the emergency crews - and there must be no compromises. That is one challenge. The other is our goal at Rosenbauer to offer the best ARFF vehicle in the world. That is why we have been constantly developing the PANTHER for 30 years and always bringing new models onto the market when requirements or standards change significantly, or new technologies become available.
How does Rosenbauer manage to keep setting the bar for ARFF vehicles?
Wolfgang Luftensteiner:There are many good reasons for this, one of which is certainly that we develop and produce the entire vehicle ourselves, from the chassis to the body, right down to the firefighting equipment, including operation. Another is that we go into the smallest detail when it comes to technical questions and have specialists in the team who have been working on the development of the PANTHER since its beginnings and therefore have 30 years of expertise. And for me, the most important thing is the enthusiasm and the lifeblood, that is the energy that the entire team invests in this product, from development and quality assurance through to production. In my opinion, you can also see this vigor in the PANTHER!
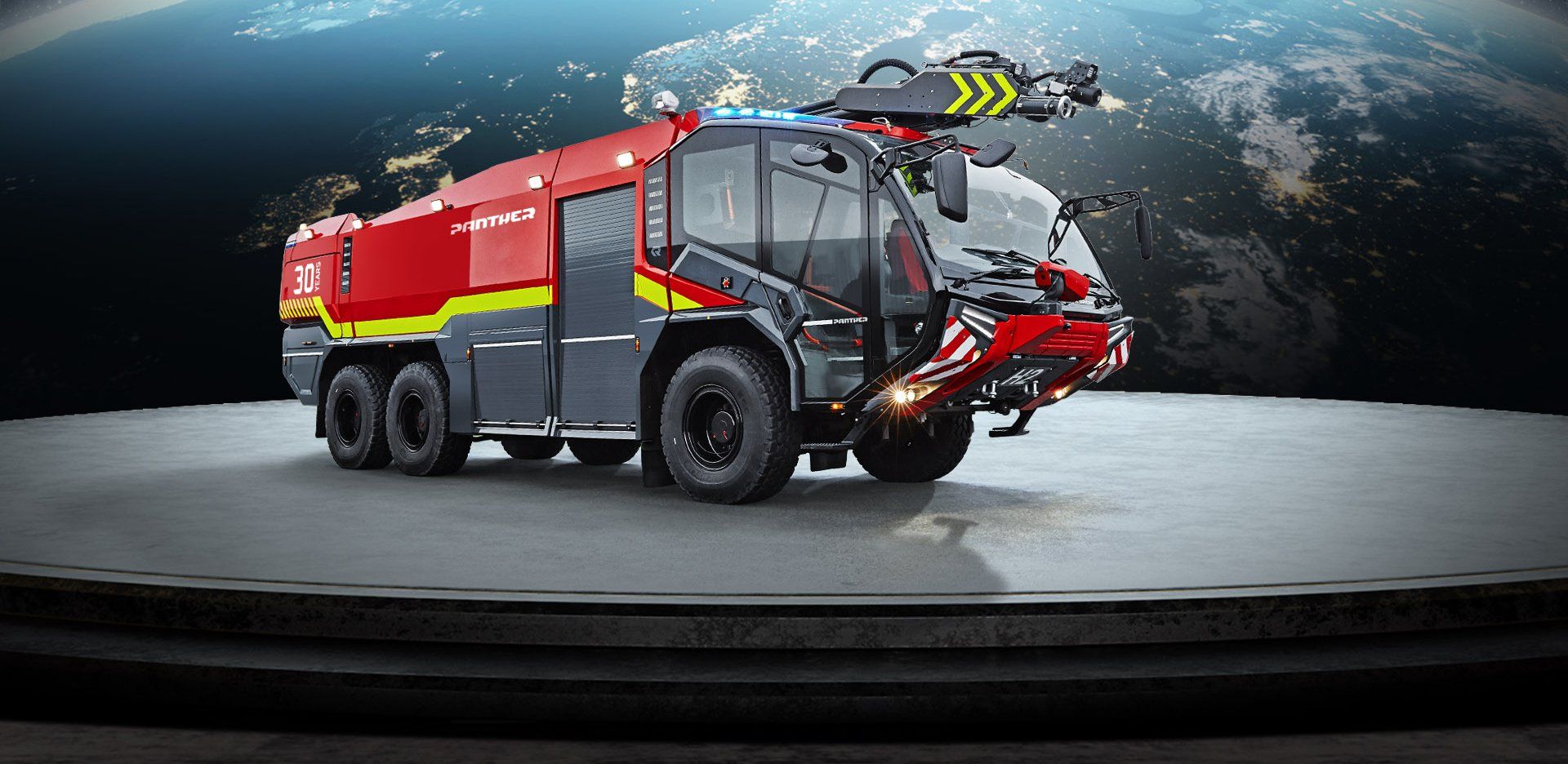
Register now for the Rosenbauer Newsletter & always be well informed!
Contact
Rosenbauer International AG
Paschinger Str. 90
4060 Leonding, Austria
office@rosenbauer.com